Overview of Stone Crusher business
The stone crushing business is an important activity in the construction industry and other related areas. It involves the manufacture of various products out of crushed stones that are used for concrete, building roads, landscaping among others. This business often includes establishing a stone crushing plant which is equipped with jaw crushers, cone crushers, screens and other processing machinery for a variety of raw materials including granite and limestone.
Due to the rapid pace of urbanization and many more construction works, the demand for better quality aggregates is growing which means that this industry has better growth prospects. Nevertheless, although it requires a high capital outlay in the beginning, this kind of business can be quite profitable provided there are effective management and demand. Therefore, this sector is most suitable for entrepreneurs who are in the construction industry.
Profit potential: Stone Crusher business profit
In India, the stone crusher business can indeed earn high profits, the size of these potential earnings depends on the scale of the operation and the state of the market. For example, a stone crushing plant which is properly managed, situated in a sound market and producing approximately five million tons of aggregates yearly, can earn profits of about two hundred million rupees annually assuming an average selling price of about 80 rupees per ton, cost of production of 20 rupees per ton, and net profit of 60 rupees per ton.
Similarly, small scale plant producing roughly 500, 000 tons in a year could make a net profit anywhere between over a million to 20 million rupee in profits something within the efficiency and demand ranges in the market. Overall, the profitability of this business is enhanced even more by looking at the construction material requirements for the rapidly developing infrastructure sector in India.
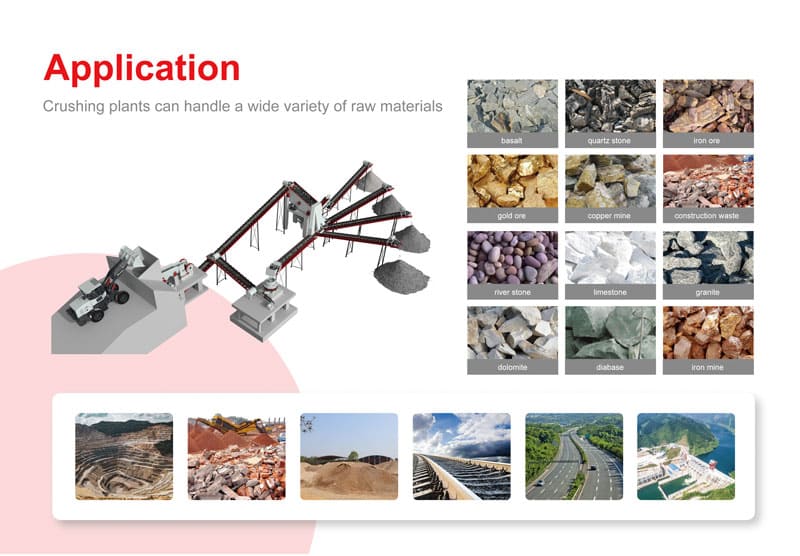
Image Credit: Daswell.com
Investment required for a Stone Crusher business | Stone Crusher plant setup cost
Starting a stone crusher business in India involves several key investments that can vary based on the scale of operations, location, and specific requirements. Here’s a detailed breakdown of the investment needed:
Stone crushing business is one of the specialized industries in India. Setting up a stone crushing business doesn’t come cheap, in fact, it comes with several key investments. The type of investment, however, can depend on a number of things including the specific needs for the business. Let’s take a look at how investments are broken down.
1. Initial Set Up Cost
- Land Acquisition: One can expect a cost for land to be in the region of about ₹20 lakhs to approximately ₹50 lakhs depending on where the construction plant is to be set up and how big it is required to be.
- Machinery and Equipment:
- Stone Crusher Machines: A complete stone crushing setup comprises jaw crushing machine(s), jaw forces crushing system (Intermediate), Stone bashing machine impactors, and screening machines. The price of these machines can vary between ₹25 Lakhs to ₹1.50 crores based upon its production and technology.
- Ancillary Equipment: Other potentially additional costs would be incurred in conveyors, feeders and several other cost additional options and these could require between ₹10 Lakhs to ₹30 Lakhs.
- Site Preparation: This encompasses carrying out cleaning, land levelling, as well as putting up required building structures and all these may amount to costs of between ₹5 lakhs and ₹15 Lakhs.
2. Operational Costs
- Volume of Labor Costs: Employing skilled and unskilled personnel can cost between ₹5 lakhs and ₹15 lakhs in a year depending on how many of such workers are to be employed.
- Electricity and Water Expenses: Mains supplies of power and water are to cost around ₹20,000-₹50,000 or so by the month.
- Maintenance Costs: Maintenance of machinery is essential; a budget of ₹2 lakhs to ₹5 lakhs per year is recommended.
3. Raw Materials
- The initial outlay for raw materials (stones or boulders) will be determined by their cost and proximity. This cost may have a wide variance but must be taken into consideration in working capital.
4. Permits and Licenses
- Authority permits that have to be obtained may attract costs in the range of ₹10,000 — upto ₹ 1 lakh depending upon regions and regulations.
5. Environmental Compliance
- The application of systems for the control of dust and other environmental factors may also needs a further capital of ₹ 2 lakhs to ₹ 10 lakhs.
6. Marketing and Promotion
- There is a need for placing certain amounts for marketing….this will assists to attract customers around 50,000 rupees to 2 lakh rupees for up to a year.
7. Working Capital
- Working capital can be utilized in the general operational activities of the business. Amounting close to approximately 10 million to 20 million is also ideal.
8. Contingency Fund
- A contingency fund of about 10-15% of the total amount invested is wiser to set aside in order to avoid unplanned expenses.
Summary of Investment Estimates
Expense Category | Estimated Cost (INR) |
---|---|
Land Acquisition | 20,00,000 – 50,00,000 |
Machinery & Equipment | 25,00,000 – 1,50,00,000 |
Site Preparation | 5,00,000 – 15,00,000 |
Labor Costs | 5,00,000 – 15,00,000/year |
Utilities | 20,000 – 50,000/month |
Maintenance | 2,00,000 – 5,00,000/year |
Raw Materials | Variable |
Permits & Licenses | 10,000 – 1,00,000 |
Environmental Compliance | 2,00,000 – 10,00,000 |
Marketing & Promotion | 50,000 – 2,00,000/year |
Working Capital | 10,00,000 – 20,00,000 |
Contingency Fund | ~10-15% of total investment |
All in all, the stone crushing startup in India requires an average of about 1 crore to 5 crores INR if the condition, scale and the location are taken into account. At this level of investment, it is advisable to carry out extensive market analysis and even develop a business strategy for this type of venture.
Stone Crusher Plant Setup – Machinery Requirements
Establishing a stone crusher form the very beginning entails incorporation of critical components and machinery pieces, whose teamwork will guarantee high levels of efficiency when handling operations as well as the production of high quality aggregates. Below is a systematic description of the design particulars in a stone crusher plant as well as into the machinery required.
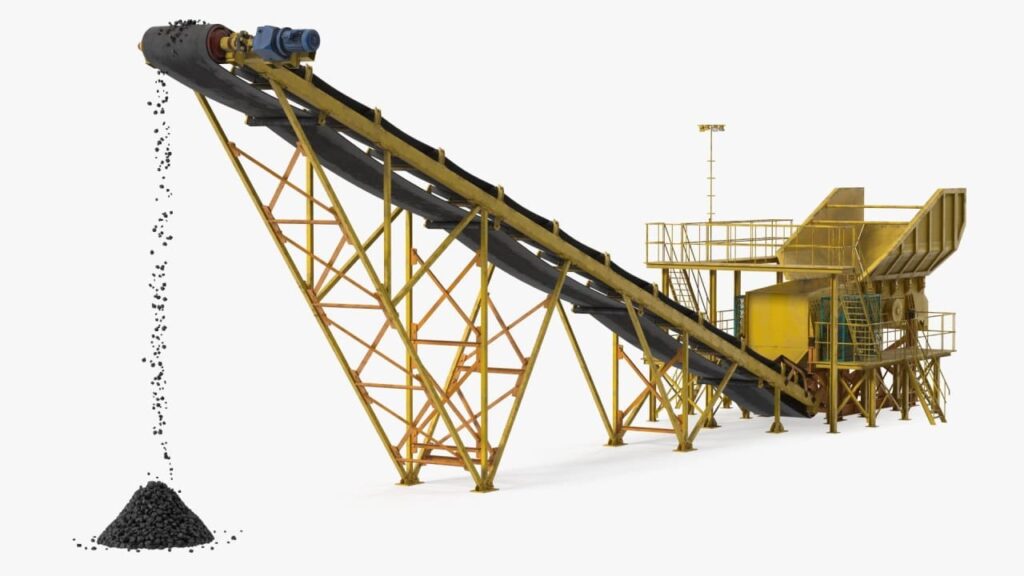
Important aspects of Stone Crusher Plant Design
When designing a Stone Crusher Plant Site, there are various considerations to be undertaken so as to enable the optimum performance to be achieved. The overarching aim while designing is on layout design, equipment selection, estimates of capacity and planning of operations workflow.
The design of stone crushers takes into account key processes so as to achieve the objectives of the plant in an efficient manner:
- Equipment Selection: Select other types of crushers based on the type of material to be processed and the size of the finished product namely jaw, cone and impact crushers. The types selected should be in relation to the production capacity needed.
- Selecting the right machine is vital. Know the material to be worked on (for instance, jaw crushers for hard rocks, impact crushers for softer materials).
- The expected output capacity also needs to be taken into account when selecting the described equipment.
- Layout Design: Plan the layout is in an ideal manner so that the movements of materials are kept to the least and so is the time taken to complete a process in the plant. This involves the location of crushers, relocation, and movements of crushers, screens and conveyor belts to enable easy flow of materials and activities to other positions or phases.
- The layout should minimize any material handling and transportation distances within the plant and the surrounding area.
- Placement of crushers, screens, and conveyors should allow for easy movement from one process of production to the next.
- Capacity Planning: Assess the required output capacity in tons per hour depending on both the market needs and the requirements of the project (e.g., between 50 and 600 tons per hour). Make sure that the chosen machines are capable of handling this capacity efficiently.
- Estimate what the target output should be depending on the possible market (e.g., 10 TPH to more than 100 TPH).
- There should be reasonable provision for alteration of the initial design of the plant if the producing capacity needs to be increased.
- Environmental Considerations: Address possibilities for dust and noise control in order to meet requirements of the relevant regulation. This may include measures such as dust suppression systems and barriers.
- Appropriate wetting agents and noise masks have to be used to meet the environmental requirements.
- There should be enough drainage systems to the design to restrain any runoff from the site.
- Safety Measures: Order the plant layout with safety as the paramount concern so that all equipment can be accessed without risk during maintenance and the machine operators can perform their duties under safe conditions.
- Provide adequate access to all equipment that needs maintenance, while ensuring that the working areas for the personnel are safe.
- Safety precautions such as safety shields and emergency cut-off systems have to be incorporated in the design.
- Testing and adjustments: Once the machine is set and installed, it is important to assess how the machine works if it was fully optimized and make relevant alterations. Proper times for servicing and maintenance of the machines should also be incorporated at all times in order to always have the machines in perfect working conditions.
- Once installed, the equipment should not remain idle, and test runs should be performed to assess the effectiveness of the equipment, and adjustments made where necessary to improve output quality and efficiency levels.
- Create regular schedules of maintenance to ensure the proper operation of machinery.
- Flexibility for Expansion: When planning the plant layout, it is crucial to take the prospects of growth into consideration: the plant should have additional capacity that would permit expansion of the equipment or alterations in future once demand increases.
- Use modern devices as automation systems for the supervision of performance as well as for the facilitation of operational efficiency.
- Try and consider the use of mobile or portable units which enable movement for convenience purposes during projects.
If these aspects are concentrated on during the design stage, an effective stone crushing plant will be achieved that produces at the desired levels and is still safe and environmentally friendly.
Machinery Requirements in a Stone Crusher Plant
The construction of a stone crusher plant sometimes referred to as a stone crushing plant is an industrial establishment which is aimed at the crushing of big stones into smaller particles/ aggregates usable for different construction works. Some of the most important machinery required include:
- Vibrating Feeder: This equipment regulates the flow of crushing raw materials into the crushing machine, also referred as the crusher machine. The equipment allows for determination of feed rates into the machines which determines the success and the rate of the crushing processes.
- Jaw Crusher: The jaw crusher is primarily used as a primary crushing machine and it is constructed to crush large large pieces of rock and break them into smaller chunks. This makes it the most important machine for the first stage of size/practice reduction.
- Cone Crusher: This tool is employed in secondary crushing stage and its role is to further reduce the size of materials that jaw crusher has processed. They are ideal for finer aggregate and their combined crushing of harder material is of higher efficiency.
- Impact Crusher: High-speed impact forces are employed in this crushing machine to provide enough strength to cut stones into very small pieces. The machine is very effective in the task of making medium symmetrical aggregates.
- Vibrating Screen: The first step in creating large aggregate sizes is by passing the initial material through the process of crushing followed by using different screens. In this way, producers are able to make products of the right size in the right time.
- Belt Conveyor: These belong to the basic units for handling operations in the plant as they transport aggregates from one stage of the process into the other.
- Electric Control Panel: It is in charge of all electric activities in the plants so that all the machines can work with ease.

Image Credit: IndiaMart.com
Additional Equipment
Further, depending on the present circumstance and specific requirements of a site, those additional equipment may be the citizens:
- Hoppers: For breaking of the raw materials by hand or storage of the materials.
- Rotary Screens: For progressive classification of materials.
- Trolleys: Used in moving the crushed material to the appropriate locations on the site of the plant.
- Spare Parts: It also includes spare jaws and other tools primarily for maintenance purposes.
A carefully planned design of technical and organizational parameters related to a stone crushing plant combined with selection of machinery functionality allows many plant operators to develop an optimal production unit to meet the required demand of the market, overall operational efficiency is acquired.
Individual Standalone Stone Crusher machines
1. Mini Stone Crusher Machine
A mini stone crusher machine is a small and powerful equipment which is used for the crushing of stones and rocks into smaller aggregates. These machines are most useful in small construction site projects, recycling jobs, or in places where large machinery is not available. Here is a closer look at the mini stone crusher machine focusing on its features, specifications and its applications.
Key Features
- Compact Size: In order to save space, the mini stone crushers are made in small sizes so that they can fit even in small locations and also be transported easily.
- High Efficiency: These units are small in size but can be able to produce high output of approximately between 1 to 20 tons per hour depending on model.
- Versatile Applications: They can be used for various materials including concrete, bricks, stones and other civil construction debris.
- Cost-Effective: The cost of purchasing the mini stone crushers is lower than that of the larger models which makes them ideal for small businesses and starts ups.
Specifications
- Material: Usually made of mild steel or high grade alloy steel to enhance durability.
- Power Source: The most common power supply for mini stone crushers is electric motors (AC motors) or diesel engines.
- Automation Grade: А large number of models are semi-automatic, of which only minimum operations are performed manually.
- Feeding Size: The feeding size is approximate 8 inches, but it can vary.
- Output Size: The size of the end product is a variable that can be adjusted to meet end user requirements, with a finish of approximately 6mm commonly attained.
Popular Models
- Vardhaman Mini Stone Crusher
- Knoxe Mini Stone Crusher
Applications
- Construction Sites: Works best for small construction works with limited area and budget.
- Recycling Operations: To crush and convert waste products into reusable aggregates.
- Road Construction: To make gravel and crushed stones that are needed for the main layers of roads.
- Mining Operations: For small scale mining operations to deal with ore in reasonable pieces.
Mobile Stone Crusher
A mobile stone crusher is effective and productive equipment designed for the on-site crushing of materials, stones, rocks and concrete. It is for these reasons that such machines are widely utilized in construction, mining, and recycling industries since they are easily transported and can work directly on job sites. Here is an informative and comprehensive mobile stone crushers guide where everything about this machinery is covered, including its characteristics, advantages, modes, and context of usage.

Image Credit: IndiaMart.com
Key Features
- Portability: Mobile stone crushers are easy to transport from one location to other through mounted on wheeled or tracked chassis. Due to this mobility, they can be set up and worked on different job sites quickly without major ground works.
- Flexibility: These machines can be fitted with a variety of crushing machinery types such as jaw, impact or cone mobile crushing and screening equipment. This flexibility allows them to be employed on different materials and projects.
- Strong Adaptability: Mobile stone crushers can be operated in difficult and isolated areas. Their design permits clients to choose whether to customize their system into a two or three stage mobile crushing systems.
- Cost Efficiency: Mobile stone crushers can perform on-site production of materials and do not have to haul raw materials to fixed plants saving much in transportation cost.
- Energy Efficiency: Diesel-electric engines or solar-based systems are utilized in many mobile crushers which helps in conserving fuel and reduces pollution.
- Safety Features: These mobile machines are provided with the safety features like emergency stop switch, safety barrier etc.; to ensure that the operators are not endangered during its functioning.
- Ease of Use and Maintenance: Operating a mobile stone crusher is not a complex process as its controls are uncomplicated thus only a short training duration is needed. Parts can be easily removed for normal maintenance operations thus minimizing idling time.
- Reliable Performance: Perfect construction helps mobile crushers to have stable performance in performance in many working conditions.
Types of Mobile Stone Crushers
- Mobile Jaw Crushers: These are essentially the primary crushers. They comprise of an upper and lower jaw, with the lower moving upwards to crush materials between the two surfaces.
- Mobile Impact Crushers: Focusing on impact forces more than pressure, these crushers can be used in second and third stages of crushing applications. They work very well to reduce soft materials to smaller size.
- Mobile Cone Crushers: Cone thickness type crushers are used to the max to reduce aggregate sizes as precisely as possible because they have a conical crush chamber which achieves exactly that.
- Tracked Mobile Crushers: These types of heavy machines contain a track rail system that helps them move effectively across challenging terrains making them especially great for use in mining activities where the site of work is not constant.
- Wheeled Mobile Crushers: These types of mobile crushers have been mounted on tires which lets the machine roam easy but tire mounted type may not be as effective on non even surfaces when compared to track mounted types.
Applications
- Construction Projects: Mobile stone crushing equipment is broadly deployed in road construction as well as building projects where high standards of aggregates are needed.
- Mining Operations: They allow for miners to process ore and rock material directly on the mine sites in an effective manner.
- Recycling: Great for the conversion of waste building materials into reusable materials.
- Infrastructure Development: Used in many infrastructure advancements to all source raw materials that are turned into concrete and aggregates for use in road base layers.
Mobile stone crushers are advantageous due to their mobility, versatility, economical, and energy-efficient features. As such, they are great assets in the construction and mining business nowadays. They can be used in different conditions while ensuring effectiveness, which is why many industries wish to improve material processing on-site.
Must Read,
✔️ How to Start Tour and Travel Business?
✔️ How to Start a Preschool: Requirements, Curriculum and Challenges
Stone Crusher Manufacturers in India
Given below are some of the best stone crusher manufacturers in India:
- Picson Construction Equipments Pvt. Ltd.
- Rocktech Engineers
- Mewar Hi-Tech Engineering Ltd.
- Kingson Crusher
- Dhiman Engineering Works
- Vardhaman Engineering Works
These manufacturers are recognized for their quality equipment and contributions to the stone crushing industry in India.
Stone Crusher Plant Project Report PDF
Download PDF file – Stone Crusher Plant Project Report PDF